Ball screw type actuators have less internal resistance due to friction and offer a greater performance for a given power input. However due to the construction, this reduced friction can allow for "back-driving". This simply means that the external force acting on the end of the actuators rod can cause the motor to turn, and would be a problem for our suspension design.
Ball Screw Drive
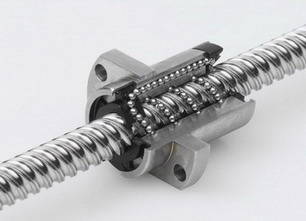
Our suspension design is predicated on the ability of the actuators to be able to control the angle of the cabin with respect to the ground, as well as support the weight of the cabin and its occupants. Therefor back driving of the actuators due to the load of the cabin could be potentially dangerous, and could occur unexpectedly with the wrong actuators installed.
To reduce the possibility of backdriving, the use of Acme screw type actuators may be a better solution. They are not as efficient as Ball Screw driven actuators, but they almost eliminate the chance of being backdriven. With safety a paramount concern in this project, it makes more sense to sacrifice some efficiency for safety. Additionally, Acme Screw driven actuators are often cheaper to produce than Ball Screw actuators, which would help minimize our overall expenditures.
Acme Lead Screw
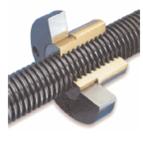
In addition to actuator sizing, the type of actuator used is one more factor we need to consider. Our group has come up the geometric design of the suspension system. At this stage we just need to make the final decision on what shocks and actuators will best suit our needs.
No comments:
Post a Comment